Design MARCH VIII
The MARCH VIII is the 8th prototype in the Project MARCH series of exoskeletons. On February the 24th, 2023, the 8th team presented the design of this exoskeleton and the challenges they face with it. The biggest challenge: making the exoskeleton walk fully dynamically and making it user-friendly. The goal is not to go faster, but to create a self-balancing exoskeleton allowing the pilot to get rid of the crutches.
Brain Control
MARCH VIII is continuing its work on electro-encephalography, or EEG, a technology that measures the pilot’s brain waves. These brain waves can then be used to determine when the pilot wants to start or stop walking, without pressing a single button. By removing interference from the signal, the EEG of the MARCH VIII is even more reliable and future proof. Such a brain computer interface opens more doors for providing a hands-free experience.
Torque Control
To control the motors more accurately in precise situations, the MARCH VIII uses new, custom-made torque sensors. These sensors accurately measure the force the motor is putting out. By measuring the forces that act upon the exoskeleton, it is possible to determine the influence of the outside world on the level of balance. By reading these outside influences, we can quickly actuate the motors to account for these imbalances.
Model Predictive Control
In order to keep the exoskeleton in balance possible missteps need to be detected quickly. Detecting these missteps quickly is essential for balance. Our new control method, Model Predictive Control, is an improved algorithm that can use the current position of the exoskeleton to predict the most balanced position of the exoskeleton in the future. By continuously updating this most balanced position every step of the way, and in between, the exoskeleton will keep its balance while walking.
Pressure Sole
Inside the sole of the shoe a new sensor is placed: the pressure sole. This sensor can measure the pressure the pilot puts onto the ground and can therefore measure how balanced the exoskeleton is. Using this data, the exoskeleton knows when and how a foot is placed on the ground. A misstep which results in only half of the foot touching the ground could lead to the exoskeleton falling, so working pressure soles is essential for keeping balance.
IMU
The Inertial Measuring Unit. Creating a balanced robot is difficult enough, but the MARCH VIII also has a human inside it. Human beings can sometimes move in unpredictable ways and using the IMU sensor we can measure these unpredictable movements. Placed on the chest of the pilot, and integrated into a user-friendly vest, this sensor can measure the orientation of the upper body of the pilot. If the pilot leans a little too far to the left, or right, our balance will change, and using the IMU we can measure this and compensate for it accordingly.
Improved Linear Joint
The joints of the exoskeleton mimic the human muscles. The linear joint does this in the hip, facilitating the sideways motion, and in the ankle, moving the feet of the pilot. This year’s linear joints are twice as fast and stronger, to handle the forces acting on the exoskeleton more easily. This is accomplished by using a new spindle; similar to the transmission of a car this transfers the energy of the motor to motion. It is now precision manufactured, meaning it can move accurately in smaller increments.
Fidlock
The MARCH VIII is fully drawn up, manufactured, and tested in just one year. During the development of the exoskeleton, a lot of tuning and changing takes place. To best accommodate for this rapid testing, we make use of magnetically attached covers. These magnets are called Fidlocks and hold the outside covers firmly in place. When a component needs to be changed for testing, we can quickly take off the cover to allow for repair and tuning.
Improved embedded system
To realize balance, a lot of new hardware needs to communicate through the embedded and electrical systems of the exoskeleton. Dozens of sensors, electronic boards, and the motors need to exchange information quickly to keep the exoskeleton in balance. Through changes made in the architecture of the embedded hardware, the system is now four times as fast. Speed that can be used to react quickly to the changing environment around the exoskeleton.
IPD
Despite the exoskeleton holding the pilot in balance, the pilot still needs to have control over their own body. The pilot can do this by using the input device, or IPD. Designed to conveniently fit the palm of the user, the IPD allows for the selection of walking modes and sitting patterns. The new IPD uses a smartwatch for its design: a device which is already optimised for wireless connection and battery life in a small form factor.
Fixtures
Offering a hands free walking experience would be nothing without comfort, and that is what the fixtures are for. The improved design focuses on increasing the contact surface of the fixture with the pilot: by creating more support, the fixture will feel more like a piece of clothing than a strap keeping you in place. As such the new fixtures are bigger, and tailor higher to the upper body of the pilot, ensuring the exoskeleton is an extension of the pilot’s body.

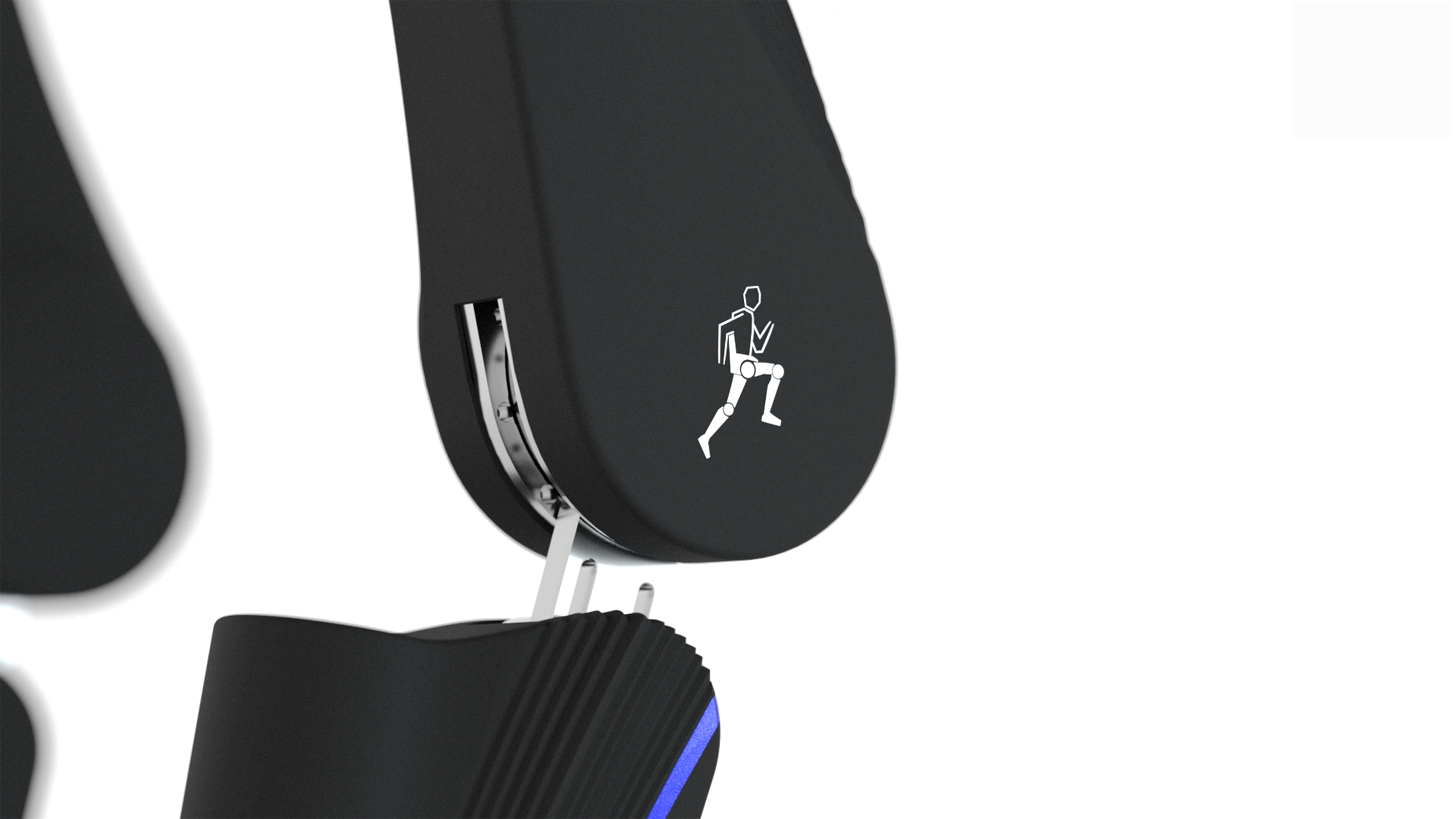
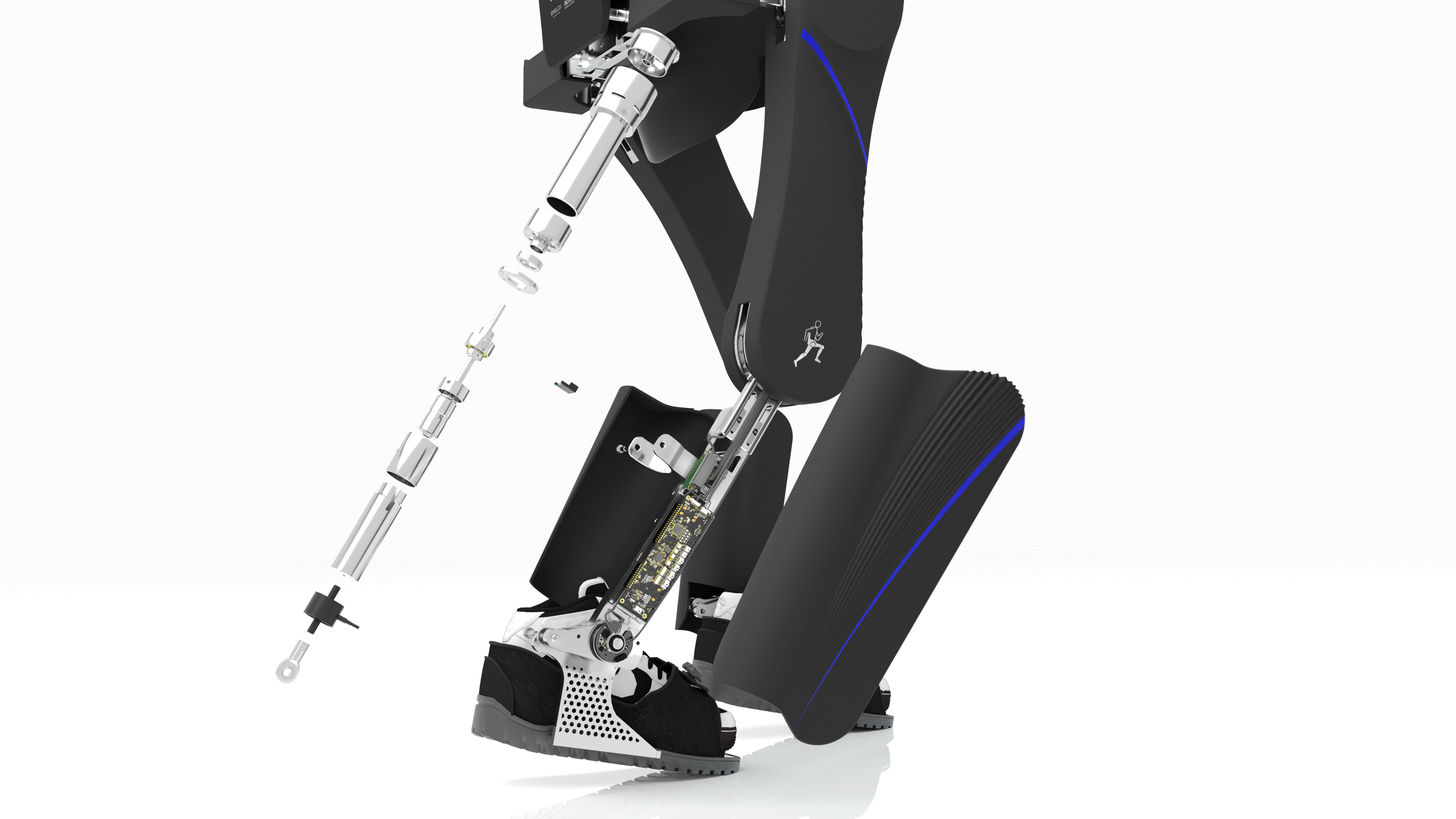

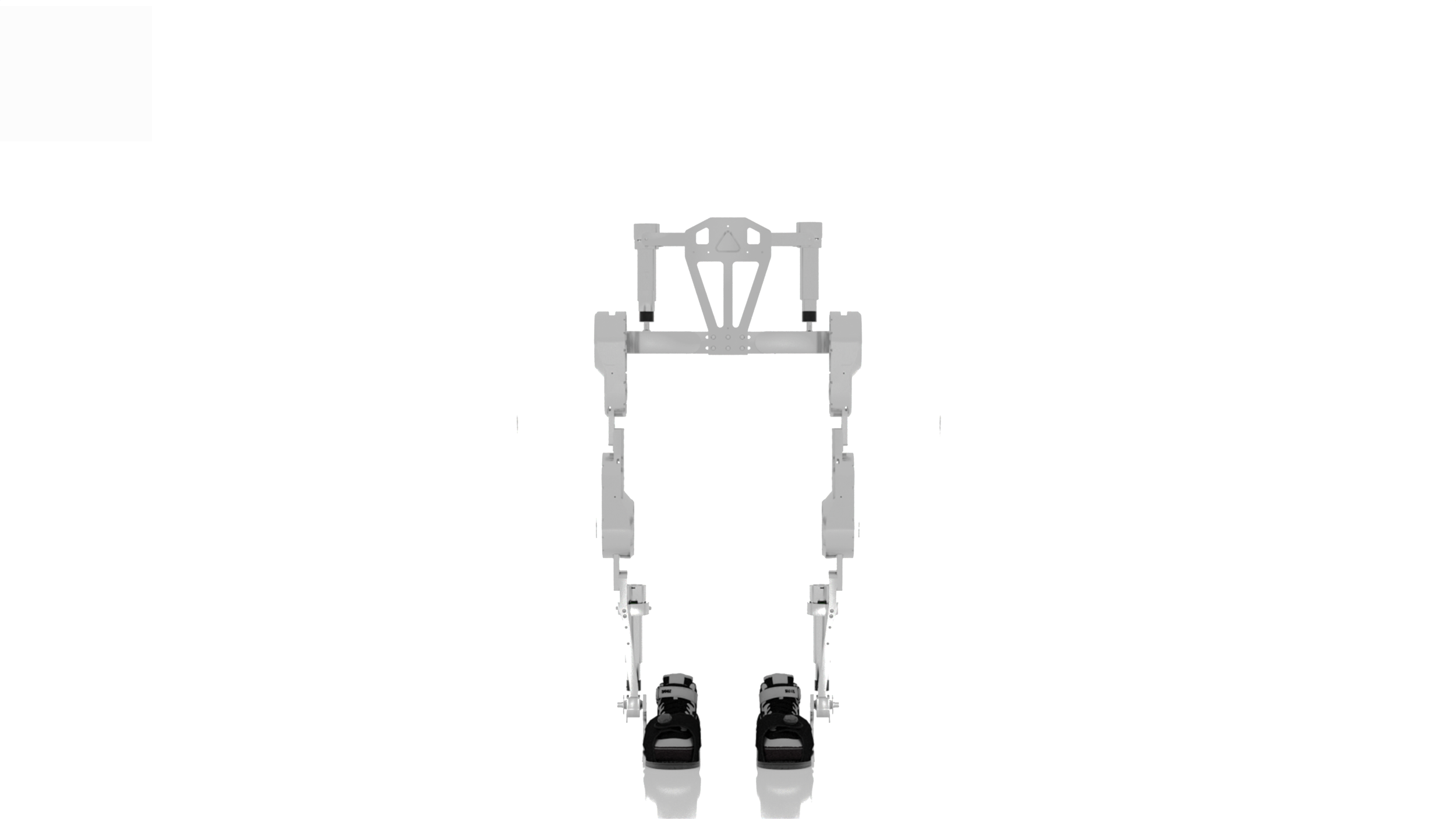
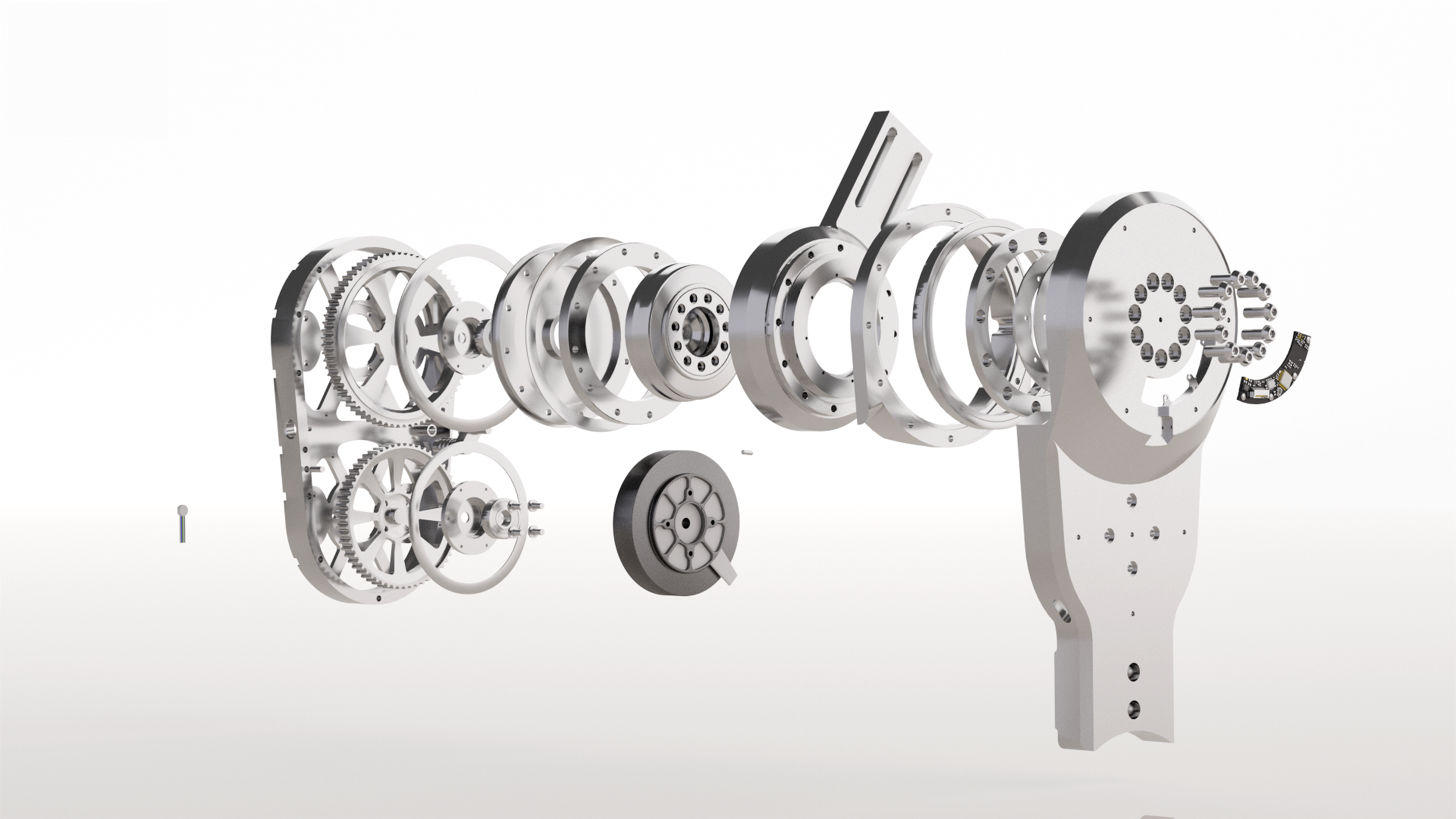